
Производственный процесс: как дизайнеру сделать свой первый продукт
Задумавшись о реализации своей идеи, начинающий дизайнер сталкивается с рядом проблем: нужно найти производство, которое возьмется за работу, найти с ним общий язык, оптимизировать затраты, следить за качеством и сроками, и сделать не один прототип прежде, чем выйти на серийное производство. Основатель компании Prokk Владимир Алексеев рассказывает, как сделать все эти процессы максимально безболезненными.
Владимир Алексеев основатель компании Prokk сотрудничал с дизайн-студиями и архитектурными бюро, занимался производством мебели, стеновых панелей и предметов интерьера для проектов офисных пространств АвтоВАЗ, Одноклассники, Mail.ru Games, KFC, Playkot, Wrike и других компаний
Основная задача дизайнера в процессе реализации того или иного проекта – это поиск оптимального решения, при котором визуальная часть согласуется с производственными возможностями и, в идеале, экономикой. Главная проблема здесь – это сложность адаптации дизайн-решений и приемов к технологическим возможностям производства и доступных материалов.
Словом, после того, как вы придумали, что хотите сделать, вам еще нужно понять, как это сделать.
Учиться – на производство
У большинства дизайнеров нет практических знаний о производственных процессах и технологиях. Пожалуй самый верный, хоть и непростой, способ приобрести такие знания – пойти поработать хотя бы несколько месяцев на действующем производстве. Так дизайнер сможет понять, как устроено производство изнутри, и получит доступ к оборудованию и рабочим рукам. Идти работать столяром не обязательно – я в свое время очень плодотворно проработал год на небольшом производстве в качестве менеджера.
К выбору предприятия стоит отнестись ответственно, иначе может выйти так, что вместо работы над интересными проектами и совершенствования своих умений, вам придется чертить одни и те же шкафы-купе и кухни бежевых тонов. Как вариант, можно попроситься на стажировку или хотя бы ознакомительную экскурсию. В этом случае можно охватить сразу несколько мест: как правило, у каждого производства есть своя специализация.
Собирайте информацию
Если возможности посвятить несколько месяцев жизни мебельному производству, нет, начните собирать информацию о разных технических решениях. Конечно, полезно посещать мебельные выставки, особенно зарубежные, но исследовать можно все что угодно: аэропорты, торговые центры, лобби отелей, торговое оборудование и, конечно, мебельные магазины – все это кладезь полезной информации.
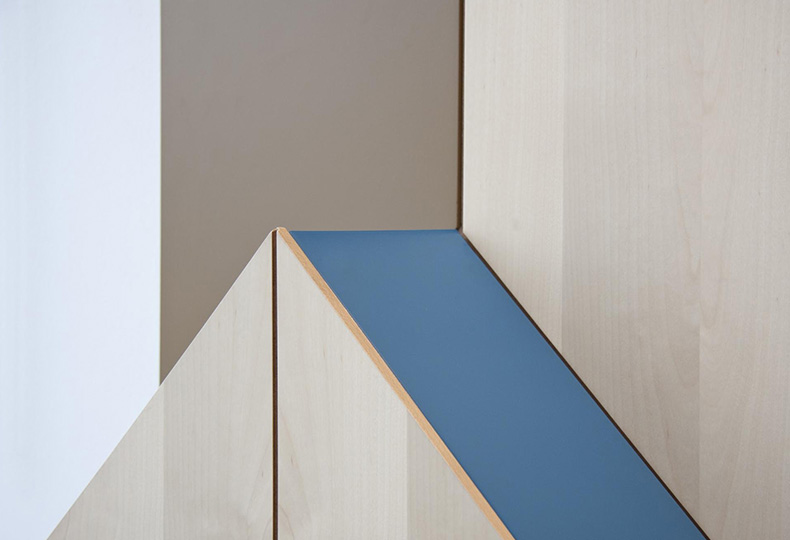
Обращайте внимание на то, как продукт сделан: из каких материалов он сделан, из каких деталей состоит, какой используется крепеж, какая фурнитура. Фотографируйте мелочи: это расширит ваш инструментарий и поможет в диалоге с производителями, которые очень любят говорить, что «так никто не делает».
Наладьте коммуникацию
Еще одна проблема производственного процесса – сломанная коммуникация между дизайнером и производителем. Это обусловлено и отсутствием четких базовых правил, и невероятной инерцией и ленью.
Изучите основы создания чертежной документации и навсегда уточните, что все размеры проставляются в миллиметрах, если материал не указан, он принимается по аналогии, расстояние до отверстий проставляются от центра и так далее. Но даже если вы чертите как бог, надо каждый раз уточнять основные моменты, так скажем, сверять часы.
Однажды мы отдали на аутсорс задачу сделать 40 столешниц офисных столов, которые потом ставились на металлические подстолья. Задача несложная: напилить и закромковать ЛДСП по заданным размерам. Но когда мы стали принимать заказ, оказалось, что с каждой стороны габаритные размеры столешниц больше на 4 мм. В итоге выяснилось, что мы дали размеры с учетом толщины кромки 2 мм (кромка в минусе), а подрядчик посчитал, что кромка идет сверху (то есть в плюсе). Доказать в такой ситуации, кто прав, а кто виноват, очень сложно – аргумент «мы всегда так делаем» непобедим. Но если бы мы изначально проговорили этот момент, не потеряли бы ни деньги, ни время. Все тонкости желательно не только проговаривать, но и фиксировать в переписке.
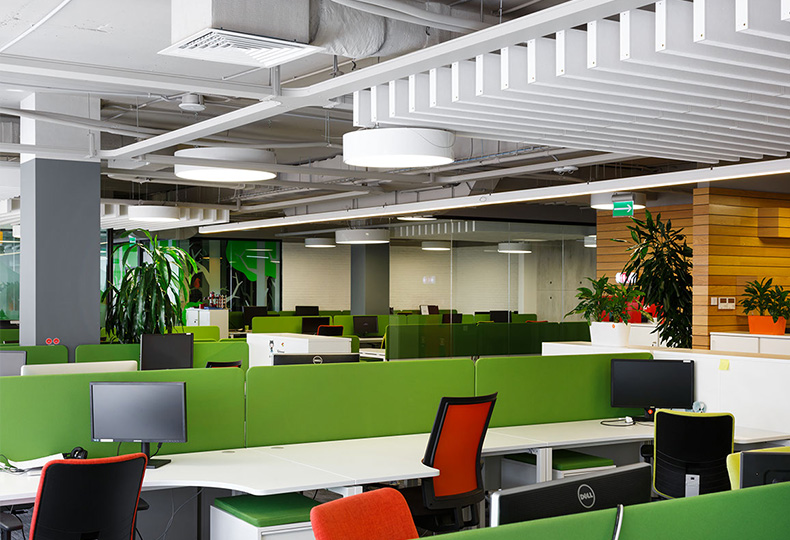
Опенспейс с теми самыми столами, со столешницами которых произошла накладка.
В самом начале можно сделать себе шпаргалки, например, по материалам: табличку с их видами, стандартными толщинами, габаритными размерами, сортностью, возможными вариантами финишной отделки, примерными ценами и так далее. Со временем вы запомните, что фанера может быть как с продольным направлением текстуры, так и с поперечным, но последняя встречается гораздо чаще, кромки имеют толщину либо 0,6 мм, либо 2 мм, у шпонированного МДФ есть два типа рисунка, порошковая краска по дефолту глянцевая, и так далее. Все это сделает процесс проектирования проще и поможет найти общий язык с производителем быстрее.
Позволять производителю самому принимать решения – особенно относительно внешнего вида предмета – опасно. Увы, его представления о прекрасном часто сильно отличаются от видения дизайнера. Внимательно отслеживайте сообщения вроде «Мы тут немного поправим пропорции, чтобы было красивее».
Не обещайте золотые горы
Часто к производителям приходят заказчики, которые завтра намерены заказать вагон мебели, но сегодня им нужна одна маленькая полочка. В ее стоимости, конечно, нужно учесть завтрашний объем, то есть сделать все бесплатно. За годы работы у нас было несколько запросов такого толка, и ни одна подобная история в итоге не случилась. Мебельное производство – это бизнес с ежедневными операционными расходами, поэтому говорите только о том, что актуально именно сегодня. Нужно сделать одну тестовую столешницу? Так и скажите. Не обещайте заоблачных объемов, стараясь замотивировать производителя, – это может сработать против вас. Если у вас и правда большие планы, сделайте оговорку о будущем, но не более. Каждому дню свои заботы.
Будьте готовы платить
Представим, вам нужно забить пять гвоздей в кусок березовой доски. Кажется, это займет пять минут и обойдется двести рублей, но с вас почему-то просят несколько тысяч. Конечно, когда все наготове, это действительно может стоить дешево, но иногда нужных материалов нет в наличии – за ними нужно ехать или заказывать доставку. Даже если вам нужно пять гвоздей и 30 см доски, купить придется пачку гвоздей и целую двухметровую доску. А еще учитывайте, что на приличном производстве всегда есть работа, и нет свободных рук – придется снять кого-то с процесса, а потом наверстать упущенное. При этом, сделать сотню самых скучных дверей производителю много выгоднее, чем пытаться воплотить вашу оригинальную идею, пусть даже завтра она соберет все медальки на Behance.
Ни одна публикация в Wallpaper или Interni не заставит арендодателя снизить ставку, поставщика сделать дисконт на материалы, а работников отказаться от зарплаты.
Кстати, у производителей есть простая схема вежливого отказа. Если нет желания браться за заказ, всегда можно умножить теоретическую стоимость производства в N-раз – если заказчик все-таки согласится, выручка хотя бы будет неплохой. Я иногда слышу от дизайнеров отзывы о неадекватно дорогих производителях – иногда это значит, они не хотят с вами работать.
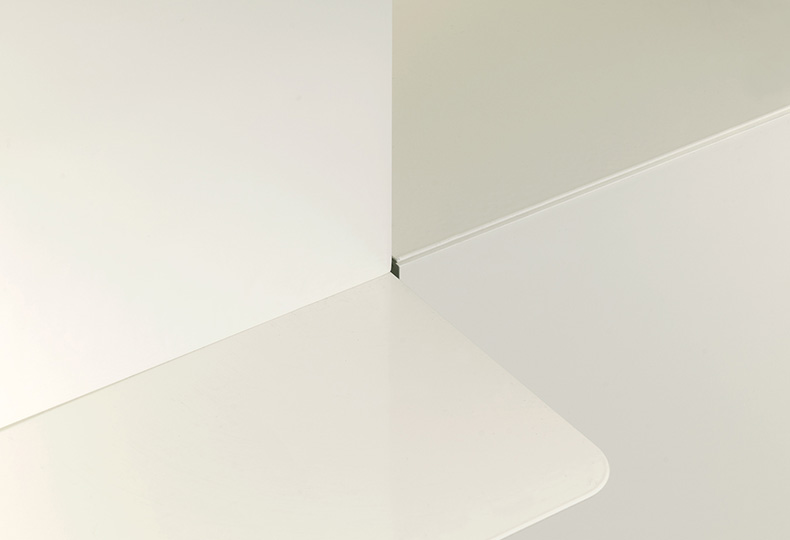
Проявляйте инициативу
В силу большой загрузки и вечной спешки производители не утруждают себя размышлениями над вашим проектом и составляет коммерческое предложение строго согласно вашему ТЗ, без раздумий на тему верны ли выбранные материалы и решения, можно ли оптимизировать процесс и тд. Запомните: вы – самое, а порой и единственное, заинтересованное лицо в создании объекта, и вся инициатива должна исходить от вас. Если отказывают в производстве, узнайте причины, попросите совета, как еще можно реализовать свою задумку. Если стоимость работ кажется вам неподъемной, узнайте, за счет чего ее можно снизить.
Может быть, у вас указан материал, которого нет в наличии, и нужно отдельно платить за доставку, но на производстве есть хорошая альтернатива? Или незначительное изменение габаритных размеров поможет существенно сэкономить на производственном процессе? Даже самые минимальные правки могут существенно снизить стоимость заказа.
Делайте вложения
Обычно при мелкосерийном, и тем более единичном производстве работает принцип Парето: 80% времени и средств уходит на подготовку к производству (разработка чертежей, расчет необходимого материала, его закупка, доставка, создание шаблонов и кондукторов, подбор выкрасок и тд), а сам процесс производства занимает оставшиеся 20% времени и средств. Начало пути всегда требует больших вложений, чем его продолжение. Зато в дальнейшем можно будет выдохнуть: имеющаяся оснастка и понимание процесса позволят заметно оптимизировать стоимость производства.
Не спешите
Если вы хотите сделать предмет, чтобы потом сфотографировать его, выложить в сеть и собрать лайки, это просто, да и фоторедакторы творят чудеса. Но, если ваша цель – сделать продукт, который можно будет производить серийно, со стабильными характеристиками и оптимизированной себестоимостью, будьте готовы к долгому и нудному процессу подготовки к производству.
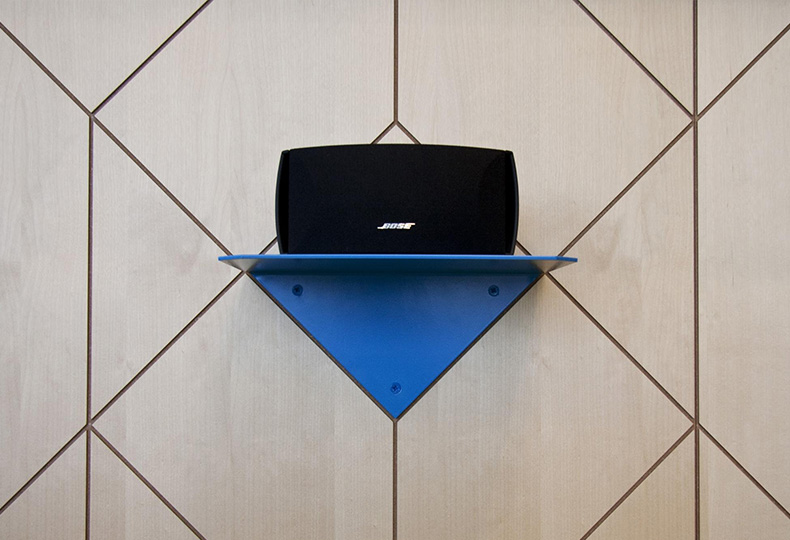
Чем сложнее конструктив и чем больше материалов предусмотрено в изделие, тем большее количество итераций понадобится, чтобы получить удовлетворительный и тем более хороший результат. По моему опыту, чтобы сделать самый простой продукт из одного типа материала, нужно по крайней мере две-три итерации – каждый раз будут появляться какие-то нюансы.
В некоторых случаях есть смысл разносить итерации во времени – чтобы изделие устоялось. Как-то мы сделали прототип окрашенной стеновой панели со сложной геометрией, а через пару месяцев обнаружил, что за счет поверхностной утяжки эмали она заметно деформировалась – значит, в конструктиве надо предусмотреть дополнительные компенсаторы. Особенно внимательно стоит работать с массивом, поскольку он живет своей жизнью.
Дьявол кроется в деталях, и в случае с мебелью эти детали – это фурнитура, крепежи, метизы и прочие элементы. Дело в том, что мебельные комплектующие – ручки, опоры, замки или соединительные элементы – на производстве обычно однообразны и не отличаются высоким качеством. Однако ощущение полноценного продукта создается, в том числе и за счет них, и в этом случае можно обратиться к таким технологиям, как 3D-печать, токарно-фрезерная обработка, литье по выплавляемым моделям, формовка и тд. Старайтесь не использовать детали из мебельных магазинов – они уменьшают ценность продукта.
От прототипа – к серии
Если вы нацелены на мелкосерийное производство, разделите процесс на два этапа. Для начала нужно будет получить прототип продукта в материале, а потом довести его до изделия. Я советую заниматься этим в двух разных местах. Для первого, идеально подойдет даже не производство, а мастерская, где фокус будет на человеке, с которым вы будете работать. Вам придется стать полноценным участником процесса производства и вносить правки прямо на ходу. Важно, чтобы ваш мастер работал с энтузиазмом, а не с постоянной оглядкой на часы. Хороший вариант – найти мастера-любителя с собственной небольшой мастерской или обратиться в мастерскую при организации. Я был знаком со столяром, который работал при художественном училище. Он делал подрамники, заготовки для студенческих работ, чинил инвентарь, и в его распоряжении была неплохо оборудованная мастерская, где он мастерил резные шкатулки в свое удовольствие.
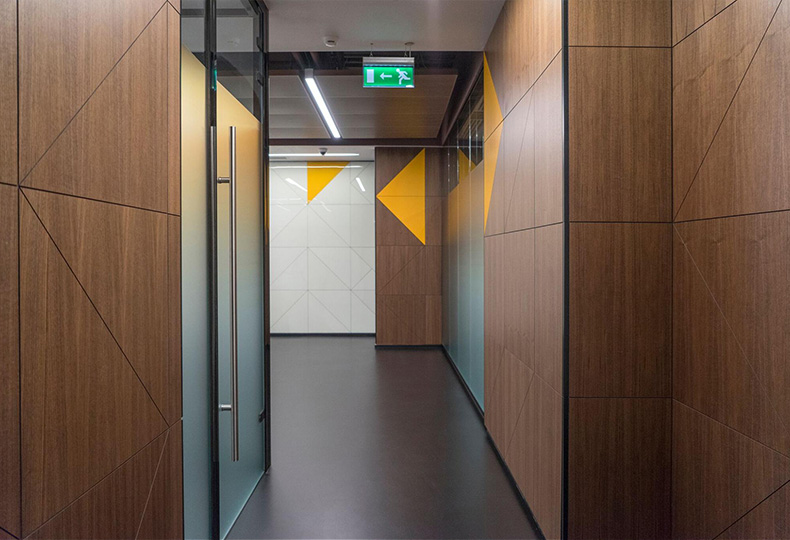
Когда вы получите изделие, которое выглядит хорошо и не рассыпается от прикосновения, можно идти на более серьезное производство, чтобы оптимизировать продукт и разработать максимально сбалансированное решение в плане конструктива и технологического процесса. Здесь завязка на людей должна быть минимальной, ведь в ходе работы вы должны получить процесс, который можно будет повторить в любой точке планеты.
Следите за качеством и сроками
Часто, доведя продукт до оптимального состояния, дизайнеры начинают получать на него заказы. В этой ситуации лучше всего полностью доверить работу производству, но если такой возможности нет, пригодятся менеджерские способности. Источники рисков – качество и сроки. С качеством все просто: инспектируйте каждый этап производства, начиная материалами и заканчивая упаковкой – чем раньше вы обнаружите брак, тем проще его исправить. Инспектируя качество материалов, учитывайте, что качество некоторых из них, например, фанеры, может отличаться не только в разных поставках, но и в одной пачке / паллете. Особое внимание стоит уделить качеству финишной отделки – она придает изделию товарный вид, и даже небольшой недочет может все испортить.
Что касается сроков, закладывайте максимальные риски на каждый этап: например, нужного материала может не быть в наличии, а транспортная компания может задержать поставки.
Разбейте на составные части
Если вы сами занимаетесь производством и хотите оптимизировать себестоимость, попробуйте разбить изделие на полуфабрикаты и разнести их по разным площадкам.
Если вы делаете все в одном месте, ваш подрядчик, скорее всего, сам отдает часть работы на аутсорс, делая накрутку на весь производственный цикл.
Некоторые операции – порошковая окраска, ЧПУ-фрезеровка, гибка металла, лазерная гравировка – дешевле делать на специализированных площадках, где цена зависит не от конечной стоимости изделия, а формируется согласно четкому прайсу. Производители же часто ориентируются не только на прямую стоимость изделия, которая включает в себя затраты на материал, человеко-часы, накладные расходы, но и на среднерыночные цены. При этом, если в изделии есть нестандартные элементы – резные узоры, сложные узлы или покраска с эффектами, – в стоимость закладывается еще и дополнительный коэффициент.
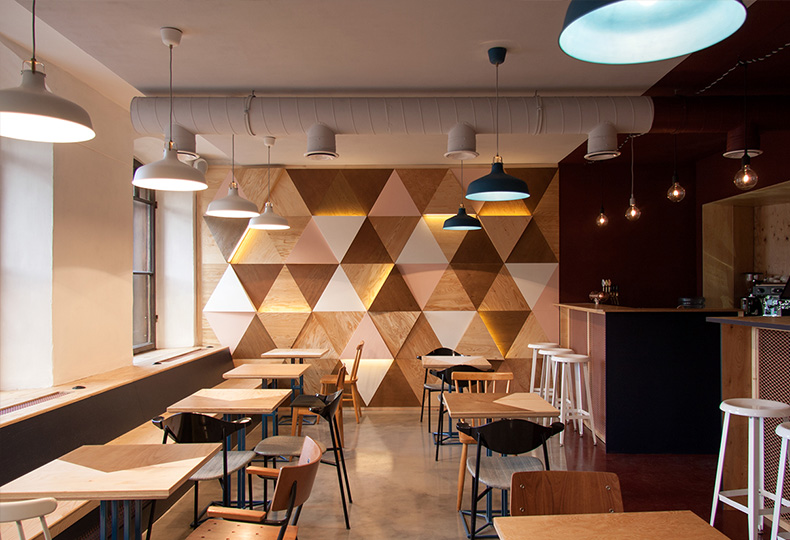
Создание мебели – это, несомненно, сложный и долгий процесс, но в то же время и крайне увлекательное путешествие, таящее в себе большое количество вызовов и открытий. Не бойтесь неудач, будьте терпеливы и помните, что профессионализм – это искусство избегать лишней работы!
На фотографиях – те проекты, в реализации которых принимала участие компания Prokk.